The automotive industry works primarily with steel. Steel is a very strong metal, but it is also lightweight. Its light weight makes it a smart material choice for use in automobile manufacturing. Vehicles are composed of many different shapes and components from engine components, axles and differential components, brakes and wheels, and the transmission and drive components to the body of the car itself.
The auto industry is all about how to cut, shape and join these various metal pieces together to form a functional vehicle. The challenge is how to do it with precise measurements in large volumes. To accomplish these tasks, the automotive industry has moved to a predominantly automated operation using CNC machining at the core of their manufacturing process. With machine tooling, the manufacturer has the ability to produce high volumes at fast rates with consistency.
CUTTING METAL
In auto manufacturing, metal is generally cut by machine. The machine operator or loader machine places the working material or piece of metal on or into a computerized machine. The operator may be responsible for programming the machine with the precise measurements to cut and shape the metal unless preprogrammed by specialist.
The most common machining tools auto manufacturers use to cut metal are computer controlled plasma cutters, laser cutters and waterjets. This is because they can cut through large volumes of material very quickly and with computerized controls there are few mistakes, and therefore less waste, and reduced production costs.
Lasers
Lasers are used to cut sheet steel up to 1/2 inch thick as well as aluminum up to 1/3 inch thick. Lasers work best on materials that are freeof any inconsistencies or impurities. Lower quality materials with a lot of impurities cause the laser to make ragged cuts and results in melted, or molten metal that splashes up and onto the laser lens.
Plasma Cutters
Plasma cutters use an ionized stream of gas that is blown past a negative electron inside the torch nozzle. The metal that will be cut is positively charged. When the gas makes contact with the metal, it results in a superheated area that ranges between 20,000 and 50,000 degrees F that effectively slices right through the working metal.
Waterjets
Waterjets use a different process to cut metal; it is called “cold supersonic erosion”.
A waterjet can best be described as a form of liquid sandpaper. A type of granular abrasive is used with the high-pressure jet of water to cut through metals and other types of materials up to 10 inches thick with a very high degree of accuracy that is critical in the automotive industry.
WHIRLING MACHINES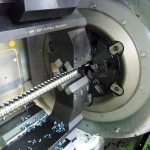
Whirling machines have increased in demand and in value for American car manufacturers. European car manufacturers have used whirling machines for more than a half-century for producing large worm gears and bone screws. Thread whirling machines have many benefits, especially when used in the machining of hard materials such as titanium and new stainless steel alloys.
American manufacturers are rediscovering the value of this machining tool because it delivers the high quality precision and quality finish required for EPS worms used in EPS steering technology commonly applied in high-end and mid range vehicles. Automotive industry whirling machines are specifically designed for high-speed cutting and multiple swivel angles to allow for almost any type of thread profile, or worm, to be produced.
GRINDING MACHINES
High capacity grinding machines are used in creating gears for automobiles. They are designed to deliver high precision products with increased productivity and shorter cycle times that previously available. Many grinders can be incorporated directly into the production line.
Many grinding machinery is now fully automated and includes gantry loaders which make it possible to place them within an assembly line since no other machines are required to handle or shift the metal work pieces. Grinders use a grinding disc that removes a little material as the disc rotates over the material. It is used to remove material along the face or circumference of the work piece.
DRILLING MACHINES
Drilling machines are used to drill holes for a variety of automotive components. Most deep hole drillers are designed for high-volume production of engine and transmission components and have CNC controls to ensure precision and accuracy. Drilling machines are used to drill openings in the work piece. The drilling machine uses a drill bit that is manually or automatically clamped. The rotation and speed of the drill bit can be varied or constant depending on the diameter and depth needed.
MILLING MACHINES
Milling machines are used to cut and drill material, most commonly metal. Millers can cut metal to create holes, smooth out sides, or create indentations so pieces of metal fit together. In the auto industry, both vertical and horizontal milling machines are used to cut and shape the body pieces as well as other components.
These mills utilize rotary motion. A milling cutter spins around an axis while a piece of metal advances through it in a way where the mill shaves off chips with each pass through the machine. Computer controls define the precise measurements required.
MECHANICAL PRESSES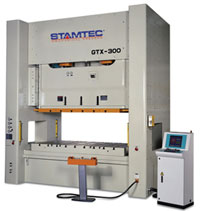
Presses are machining tools that are able to change the form or shape of a work material by applying pressure. Typical types of presses include press brakes that bend sheet metal into shape. Punch presses are used to form holes and a stamping press shapes or cuts metal by using a die. Each type of press is used in an auto manufacturing production line to perform different tasks.
SUMMARY
Machining tools have made it possible to automate almost the entire automobile manufacturing process. The tools are needed to ensure the quality, consistency, precise measurements and the high volume production of parts in the automotive industry. Automation with machine tools has made automobiles easily available and much more affordable to a greater number of people throughout the world.